MMC: driving faster, greener delivery
The proposed gains on offer for successfully harnessing modular construction are in plentiful supply. Increased productivity, decreased carbon footprint, and a means to address the skills shortage whilst simultaneously increasing building capacity.
In a bid to capitalise on Modern Methods of Construction (MMC), and secure these benefits, the Government outlined in the Construction Playbook a new expectation for departments and Arm’s-Length Bodies (ALBs) to set targets for the level of use of MMC in the delivery of projects and programmes.
The Department for Business Energy and Industrial Strategy (BEIS) and Infrastructure and Projects Authority (IPA) are developing a common set of metrics to better understand, measure and improve the performance across government construction projects.
But presumption is not a requirement, and whilst public sector ‘MMC frameworks’ are growing, there is still work to be done to dispel many of the myths around modular, offsite construction.
Barriers and opportunities
At Morgan Sindall Construction, we’ve been doing our own research into MMC - and modular construction in particular - to look at the barriers and opportunities for adopting best practice.
As part of this, we held a round table event with a team of expert consultants and customers to discuss the factors holding modular construction back; and what they would like to see happen to support wider adoption in the industry. From this event, 46% of attendees stated the biggest barrier is ‘poor perception of quality,’ with 41% articulating that ‘industry capacity for modular’ follows closely behind.
Through these focus groups and round tables, many of the participants agreed that whilst it is right for the industry to target higher adoption rates of MMC (in the fashion of what gets measured gets done!), it must still be fit for purpose.
When starting out with that blank sheet of paper, it’s important not to push modular because it’s currently under the government spotlight, but let a project’s value drivers, and the market, dictate the construction method.
Our recently published white paper Modular Construction: Have we reached a tipping point addresses research with relevant thought leaders, and subsequent research polls from the report have shown 86% suggest it should be seen as just one option – only selecting it if it is truly the best option.
Talking of these value drivers, there have been some incredible examples of modular being used exceptionally well, where it has even outperformed our own expectations.
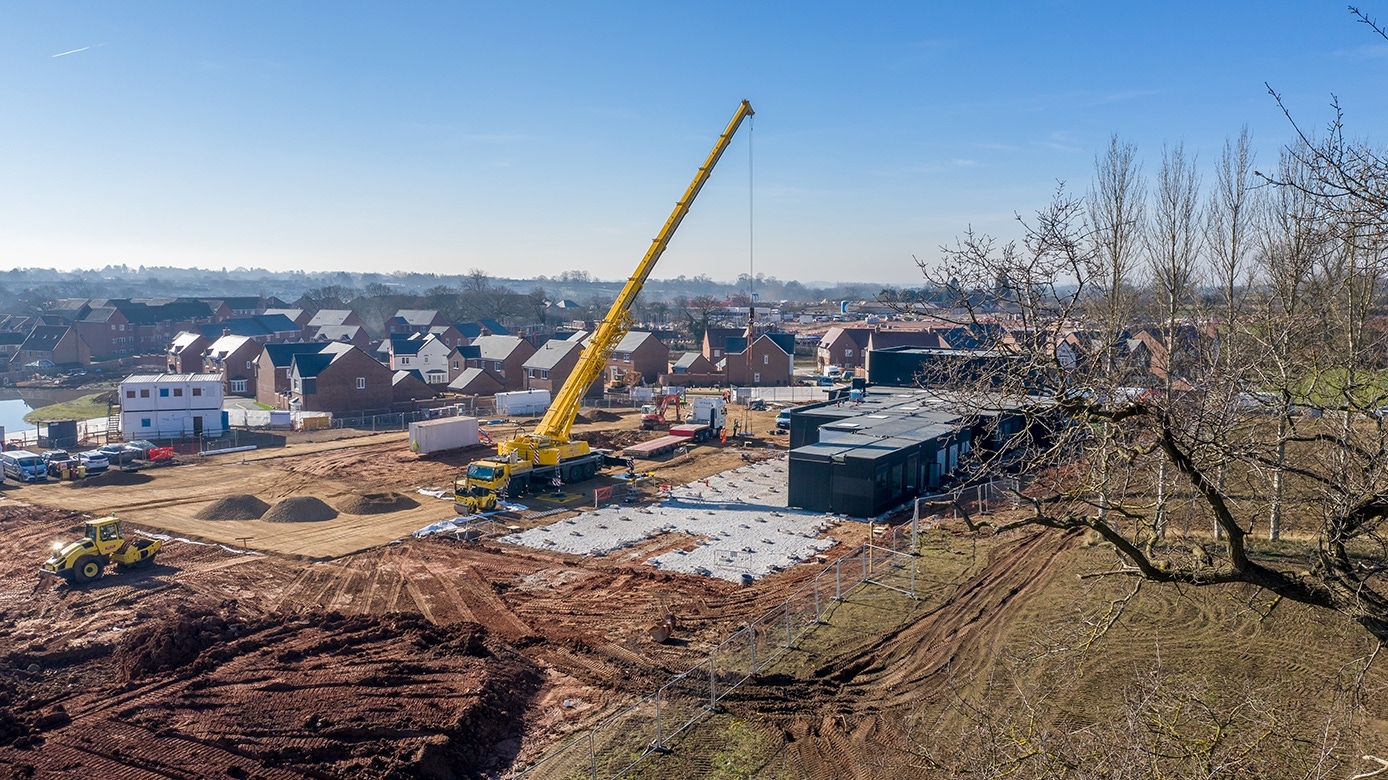
When modular delivers a better way
The first, Hackwood Primary Academy, was delivered in just 37 weeks – helping meet both local demand and Section 106 funding deadlines, whilst breaking industry records.
Similarly, when the Highfields Farm housing development in Derbyshire increased in pace (as the number of housing developers on site doubled from two to four), the need for school places accelerated exponentially creating an even shorter deadline for designing, building and opening the school.
Cue modular - and working again with Lungfish Architects and Eco-Modular, we were able to deliver the school in just 44 weeks, meeting the school place demand deadline outlined in the Section 106 agreement.
Pace was a key element with both schools, but these two projects also delivered legacies far beyond this achievement. A combined £3 million in social value was invested in their communities, and customer satisfaction scores topped out at 10/10. Both were delivered on budget, and they achieved incredible educational outcomes for the staff and pupils, helping to dispel any ‘modular myths’ that may have been present.
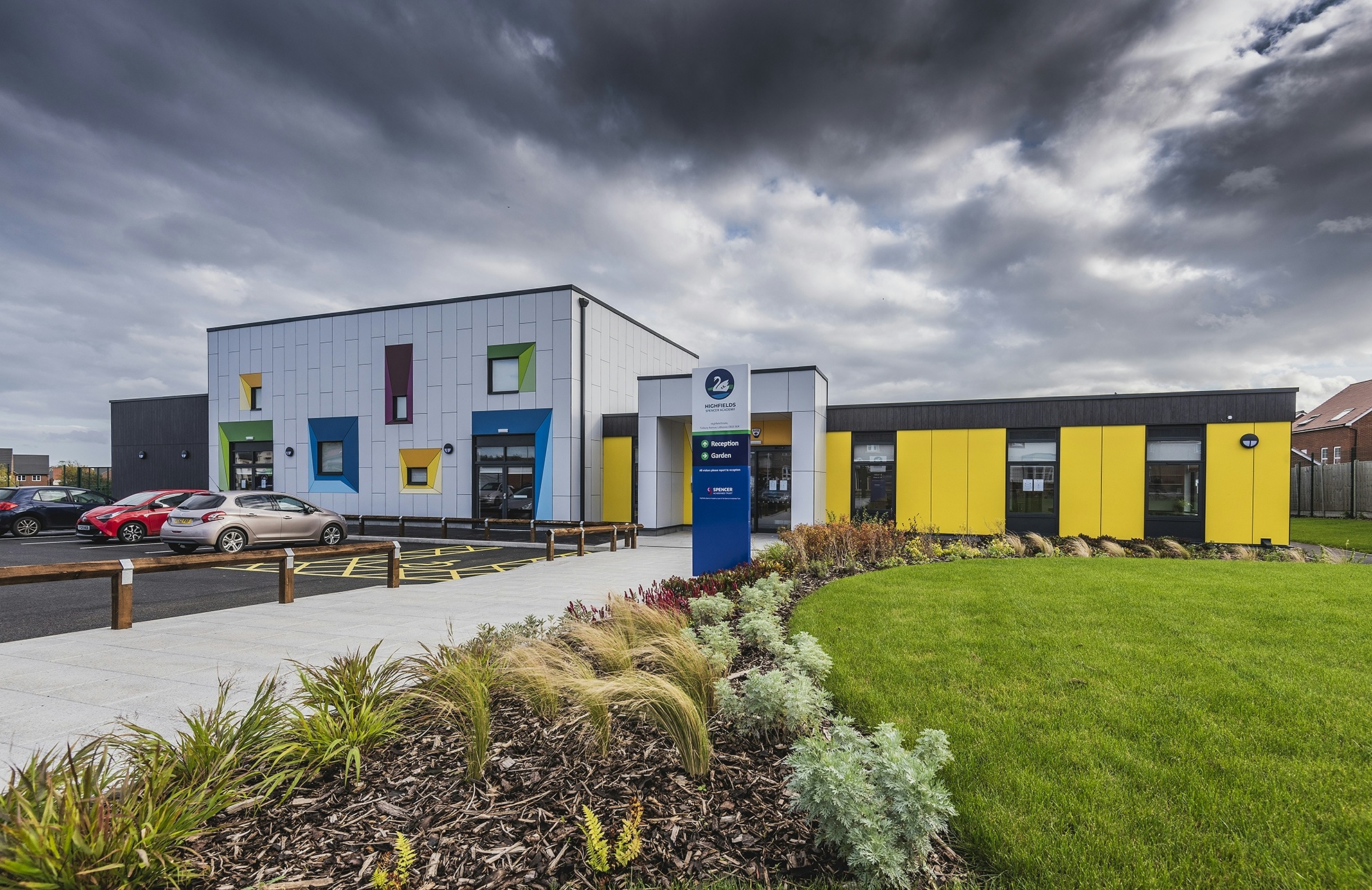
Highfields is a magic place already; the building is beautiful. The education design is so well considered, and the space lends itself to be a really positive space for children."
Anna Jones
Principal, Highfields Spencer Academy
Anna continues:
"For me as a headteacher, the experience was really positive. It had a great team and they did everything possible to make sure I was involved. We want it to be somewhere the children love coming to every day and the best example of that was one of our pupils asking their parents to drive past the school on a Saturday because they were sad it wasn’t open at the weekends. We’re so proud of it here.”
More than just pace
But modular construction has also helped us respond to other value drivers as well.
At the James Paget University Hospital in Norfolk, we delivered a fully modular 14-bed majors department with associated facilities, in just a matter of weeks, to get this key facility up and running during the pandemic.
Following a devastating fire at Ravensdale Infant and Nursery School in Derby, we were appointed to help re-build the school with the design expertise of Lungfish Architects. We were also keen to work with the community within the school, who were understandably devastated by the fire and had been temporarily re-housed by multiple schools across Derby.
Through SCAPE’s collaborative network, we were quickly able to link Derby City Council with Nottinghamshire County Council and Arc Partnership to move a temporary modular school we had built at a Nottinghamshire school, straight to Derby City’s Ravensdale School.
This allowed for the school's nursery pupils and one year group to return to Ravensdale, whilst the remaining groups were temporarily housed at Hackwood, Highfields and Castleward - three other schools we have recently built with SCAPE and Lungfish Architects.
Looking to the future
Admittedly this story is one that weaves around a number of projects, but for me it not only shows the power and speed of modular to help the industry achieve great things, but also how it can be enhanced even further when you are working within a collaborative network such as SCAPE’s – and for that I think the pupils across Nottinghamshire and Derbyshire are truly grateful.
The interconnectivity of MMC and collaboration is something I don’t believe can live in isolation. Indeed, the Ravensdale Infant and Nursery School project is one that is already taking the learnings from Hackwood and Highfields to further enhance the method of construction delivery. Standing still simply isn’t an option.
But, to return to one of the key takeaways from our modular construction white paper “fit for purpose” – I believe we are seeing a big tipping point for MMC, and modular construction in particular. More often than not now, the conditions for the selection of modular construction are being met, and they’re delivering powerful outcomes for customers, end users and importantly, their communities.
Whilst it’s always one of the options for us when delivering new buildings, our modular construction journey really has opened a lot of eyes. Not only by delivering outstanding pace, but through such a high level of finish too.
Mark Lowe
Property Capital Projects & Maintenance Manager, Derby City Council
Mark continues;
However, it’s the educational outcomes that matter most, and at Hackwood and Ravensdale, we’ve seen this become a golden thread throughout and it has reinforced our belief that there really is an interconnection between its pace and collaboration to achieve outstanding educational outcomes.”
To read more about our modular construction insight, click here to access our whitepaper.
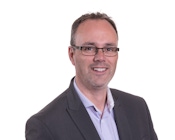
Written by:
Rob Cant
Framework Director
Related news

How do SCAPE frameworks ensure competition and procurement compliance?
28/08/2025

Tier 1, Tier 2 and Tier 3 construction contractors – what’s the difference?
20/08/2025
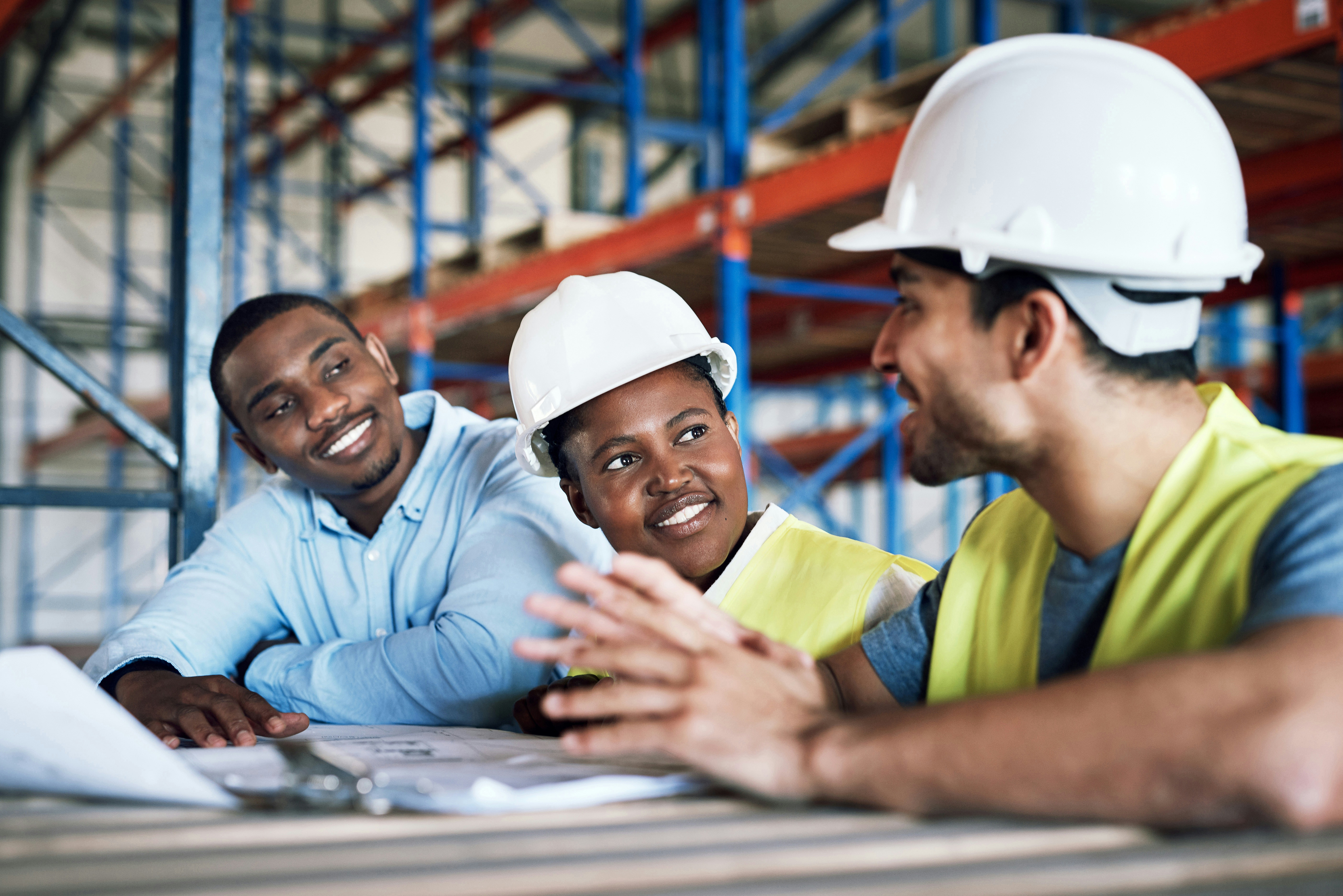
How do I manage risk in my construction project?
22/07/2025